Casting Gold & Silver
The gold casting process involves the following steps.
Wax model and casting preparation:
Using the design, a wax model is carved or printed to represent what the finished piece will look like in three dimensions. These are connected to a wax stem by a sprue. This will form the channel through which the molten gold will flow once the mold is created.
Investment:
The wax stem and the attached models are placed in a special frame called a flask and surrounded by an investment material. Once the investment material sets, it hardens into the mold for the jewelry.
Burnout:
After the investment material hardens, the flask is placed in a special kiln to burn away the wax, which leaves a cavity in the investment material that becomes the final mold.
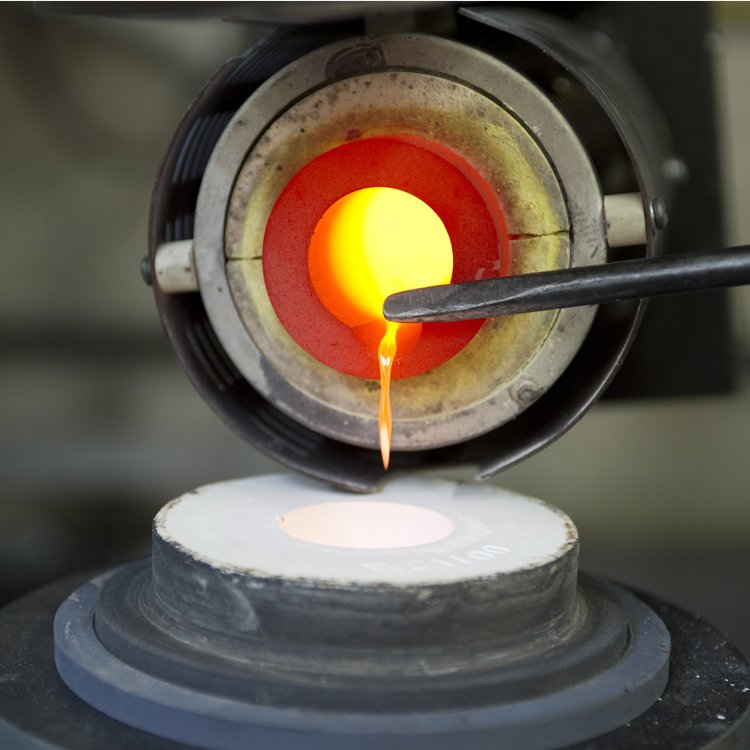
Melting:
The gold is melted, and depending on the alloy or type of gold used, temperatures can range from 1,617 degrees Fahrenheit and 2,006 degrees Fahrenheit. Gold can be combined with other metals like silver, copper and palladium to create different alloys of varying color and hardness.
Casting:
The liquid gold can be poured directly into the mold, but various techniques can be used to ensure a higher-quality casting. Centrifugal casting, vacuum-assisted casting or pressure casting can be used to ensure the gold flows into every area of the mold evenly.
Divesting:
Once the metal cools, it needs to be removed from the investment material. This can be done through physical or chemical means. Each casting is cleaned and polished, and the sprues are cut off for recycling.
“Some People Are Worth Melting For”
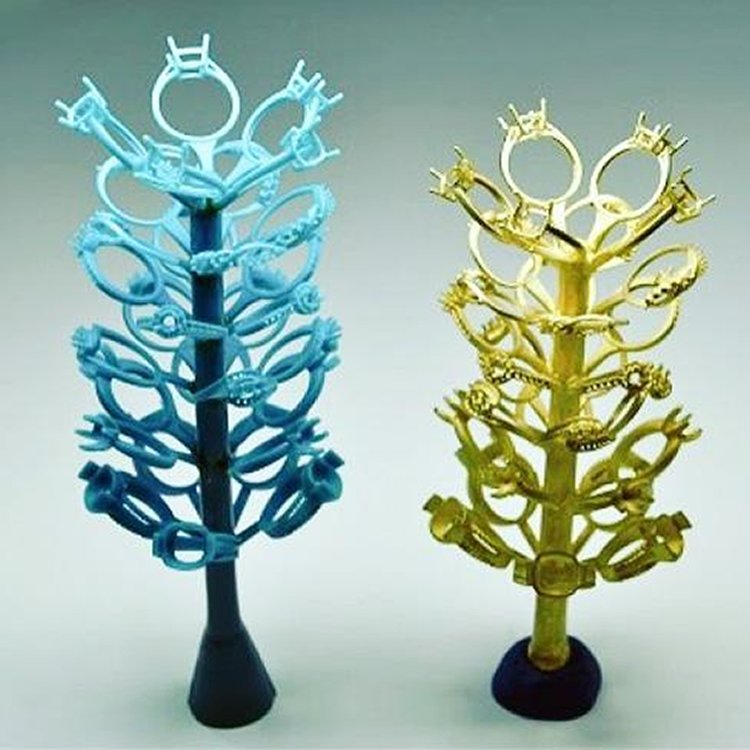